Workholding in a new dimension
The new modular workholding system for machining applications
of plates and large components.
The completely new product line Makro•Grip® Ultra offers various clamping possibilities and can be changed quickly and easily at the same time. Thanks to the expandability of its modules Makro•Grip® Ultra is capable of clamping parts of 810 mm length and beyond safely.
With its size it pushes the LANG workholding to new heights. Different system heights, individually expandable clamping ranges, interchangeable clamping jaw types and useful accessories – Through its wide range of possible configurations Makro•Grip® Ultra covers any imaginable clamping application.
Clamping jaws
3 jaw types for different fields of application:
- Serrated Makro•Grip® Ultra 125 clamping jaw, or
- Avanti base jaw for utilization of a hardened top jaw with plain clamping surface, or
- Avanti top jaw for pre-machined profiles
Threaded cap
- Secures each clamping jaw individually and indepentently from one another
- (Removal of threaded cap) Allows position change of jaws without spindle actuation
- Ensures quick jaw adjustment
Base body
- 3 different system heights (45 / 109 / 189 mm) in 2 different lengths
- Clamping ranges of 410 / 610 / 810 mm are realized putting base bodies together in different compositions
- Exceptionally high centering accuracy and exact spindle seat
- Practical snap-in function to locate the jaws quickly
Spindle
- Available in 3 different lengths for clamping ranges of 410 / 610 / 810 mm
- Equally suitable for single-part and multiple clamping
- Customized solution for clamping ranges beyond 810 mm possible
Zero-Point
System
- Quick•Point 96 as an interface between machine table and Makro•Grip® Ultra
- Consistent 96 mm grid allows to add base bodies in x-/y-direction to increase the clamping range
- High positioning accuracy of < 0,005 mm
The workholding system at a glance
Other advantages of Makro•Grip® Ultra
Convinced by the benefits of Makro•Grip® Ultra?
Then simply use the contact form to ask
for your individual quote.
Product overview
Ready for any clamping application
Modularity, flexibility and precision - Makro•Grip® Ultra
combines all these attributes in totally new dimensions.
Modular design
Innovative jaw adjustment
Easy to maintain
Quick to set up
Various center options
Low-vibration clamping
All-around machining
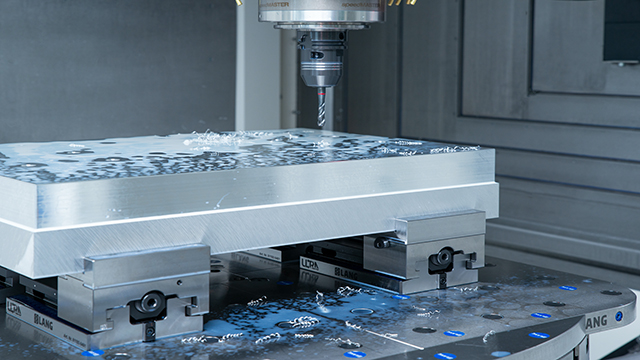
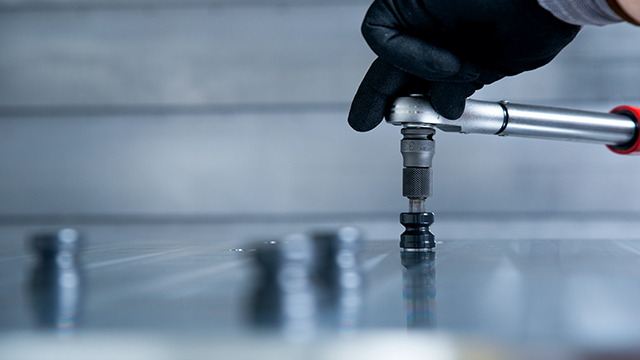
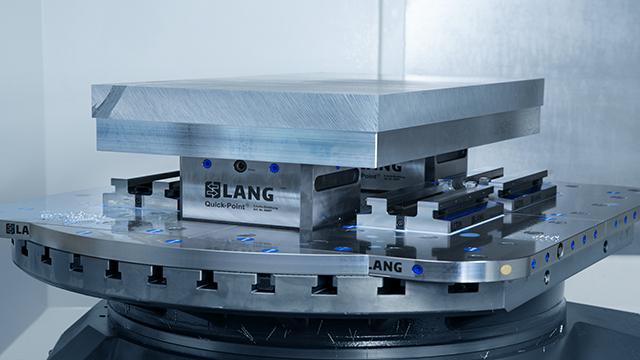
Multiple clamping
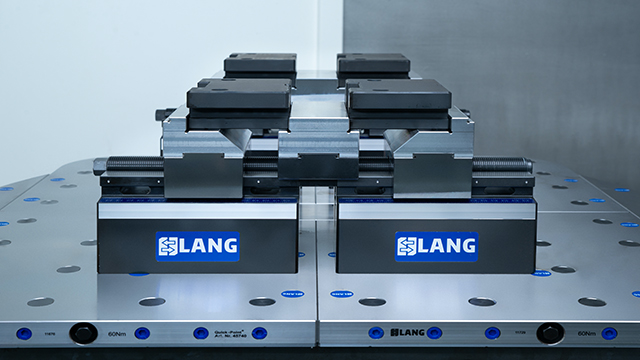

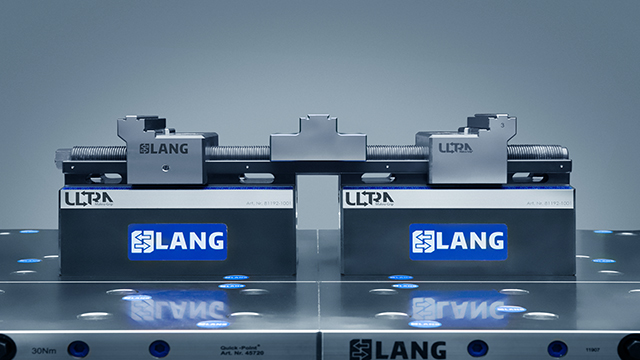
Asymmetrical parts
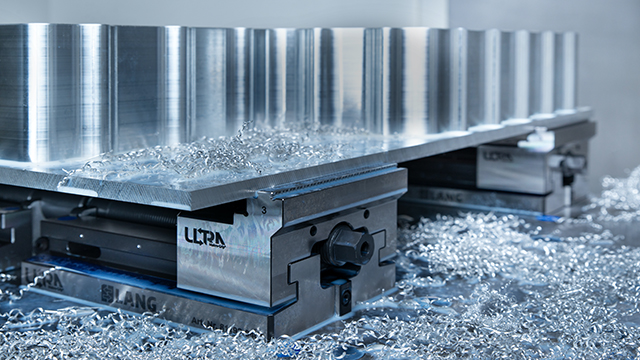
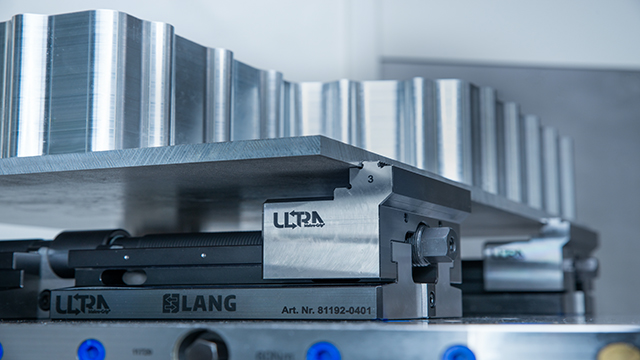
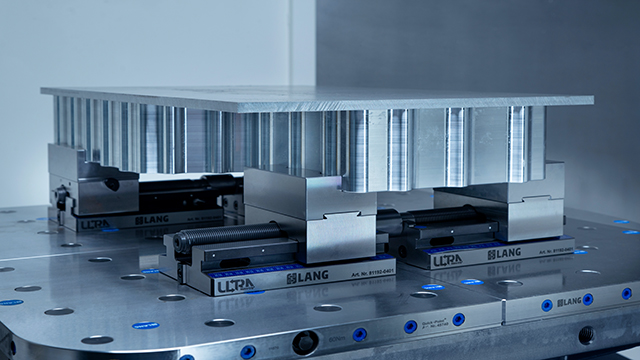
Manual and automated manufacturing
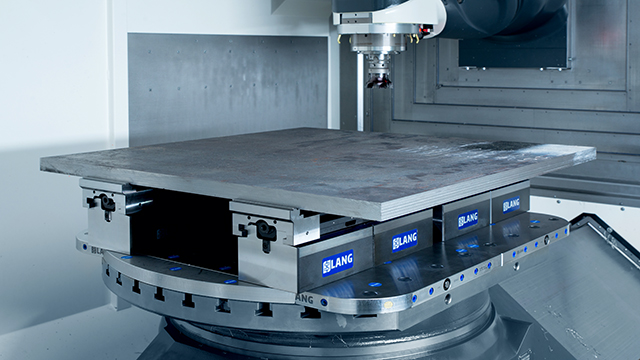
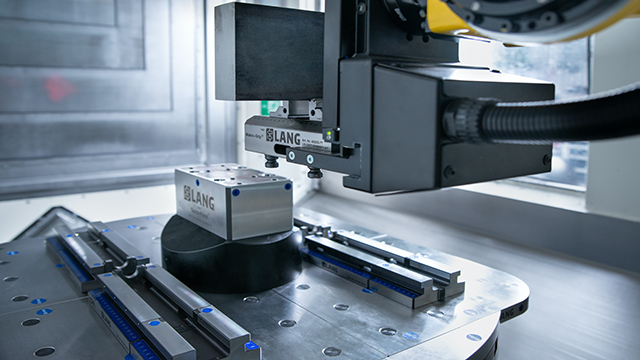
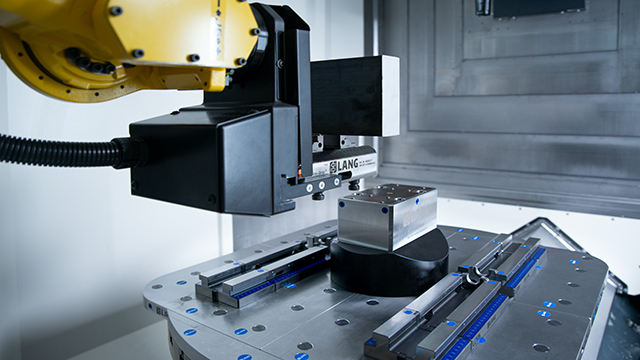
Individuell kombinierbar
Erleben Sie, wie schnell und vielfältig sich Makro•Grip® Ultra kombinieren lässt.
Clamping of large parts Clamping of asymmetrical parts Clamping of multiple parts Clamping of round parts Clamping of plates and flat partsYour connection is too slow to show the interactive 3D model. You are seeing the mobile version.
Clamping of large parts

This clamping situation consists of:
- 2x Base Set 410 L for a clamping range up to 410 mm
- Serrated Makro•Grip® Ultra 125 clamping jaws, clamping depth 3 mm
Clamping of asymmetrical parts

This clamping situation consists of:
- 2x Base Set 610 M for a clamping range up to 610 mm
- Avanti 125 base jaws and top jaws with plain clamping surface
- Unequal jaw positioning
- Avanti center base jaw with support jaw
Clamping of multiple parts

This clamping situation consists of:
- 2x Base Set 610 M for a clamping range up to 610 mm
- Serrated Makro•Grip® Ultra 125 clamping jaws, clamping depth 3 mm
- Serrated Makro•Grip® Ultra 125 center jaws for clamping multiple parts
Clamping of round parts

This clamping situation consists of:
- 1x Base Set 410 S for a clamping range up to 410 mm
- Base jaws with Avanti 125 top jaws
- 2x Hydro•Sup screw jack
Clamping of plates and flat parts

This clamping situation consists of:
- 2x Base Set 810 M for a clamping range up to 810 mm
- Serrated Makro•Grip® Ultra 125 clamping jaws, clamping depth 3 mm
Experience with one click, how easily and quick clamping applications can be changed with Makro•Grip® Ultra.
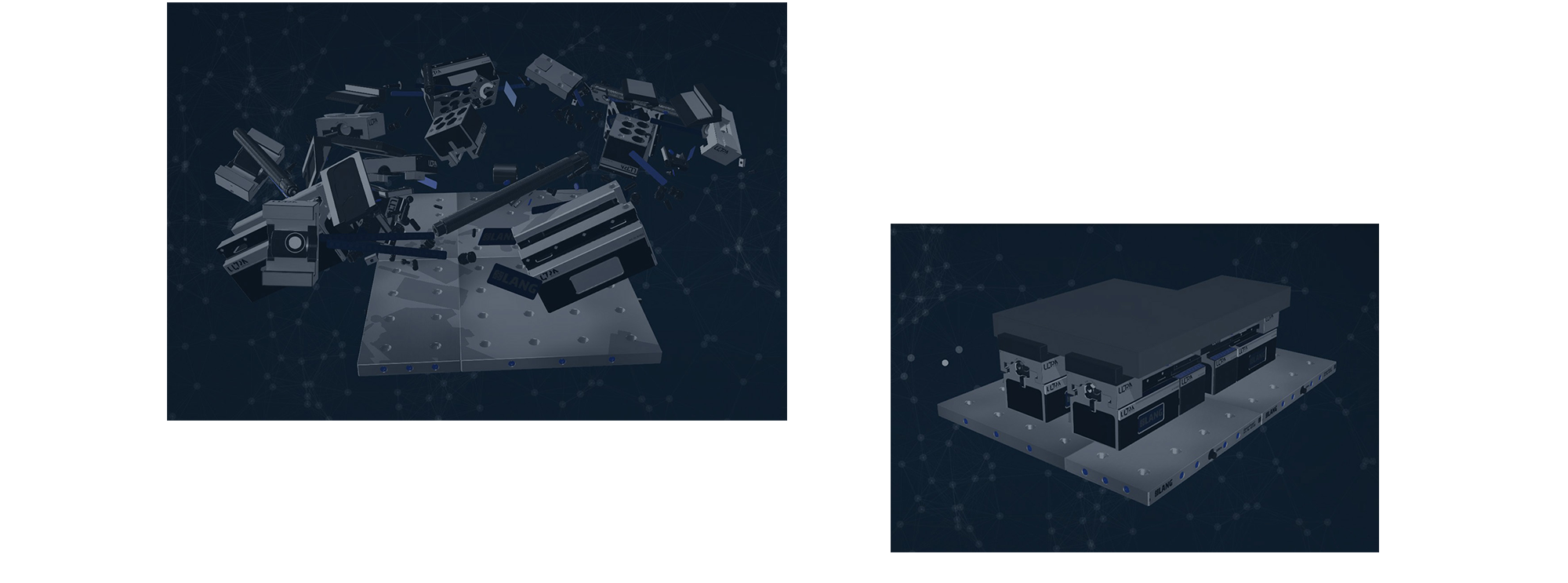
Just one moment please. The 3D model of the Makro•Grip® Ultra is loading ...
Part: 400 x 400 x 250 mm
Selected configuration:
- 2x Base Set 410 L for a clamping range up to 410 mm
- Serrated Makro•Grip® Ultra 125 clamping jaws, clamping depth 3 mm
Part: 600 x 400 mm (asymmetrical)
Selected configuration:
- 2x Base Set 610 M for a clamping range up to 610 mm
- Avanti 125 base jaws and top jaws with plain clamping surface
- Unequal jaw positioning
- Avanti center base jaw with support jaw
4 Parts: 180 x 130 x 100 mm
Selected configuration:
- 2x Base Set 610 M for a clamping range up to 610 mm
- Serrated Makro•Grip® Ultra 125 clamping jaws, clamping depth 3 mm
- Serrated Makro•Grip® Ultra 125 center jaws for clamping multiple parts
Part: Ø 400 mm
Selected configuration:
- 1x Base Set 410 S for a clamping range up to 410 mm
- Base jaws with Avanti 125 top jaws
- 2x Hydro•Sup screw jack
Part: 800 x 600 mm
Selected configuration:
- 2x Base Set 810 M for a clamping range up to 810 mm
- Serrated Makro•Grip® Ultra 125 clamping jaws, clamping depth 3 mm

Diverse configurations
Base Sets
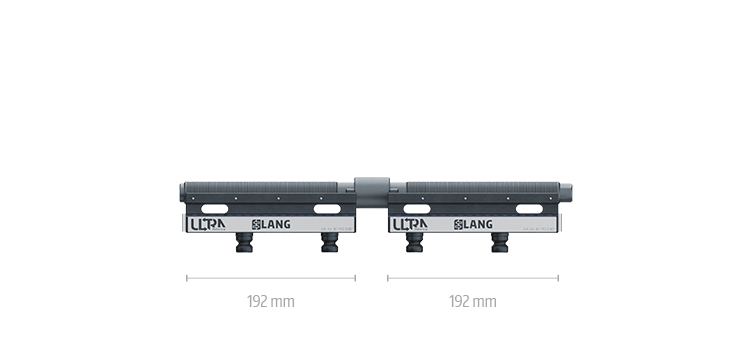

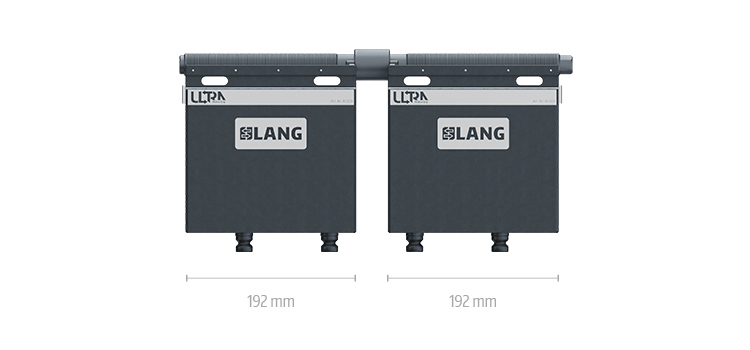
Base Set 410 S
Clamping range up to 410 mm
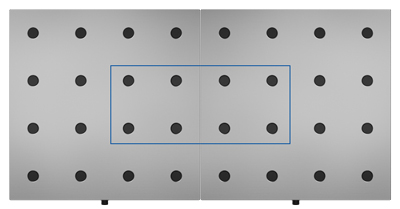
2 Quick•Point® zero-point units This graphic shows an exemplary plate configuration. Other zero-point plate types are also possible.
Base Set 410 M
Clamping range up to 410 mm
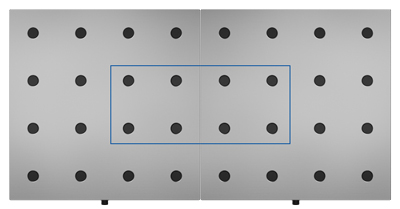
2 Quick•Point® zero-point units This graphic shows an exemplary plate configuration. Other zero-point plate types are also possible.
Base Set 410 L
Clamping range up to 410 mm
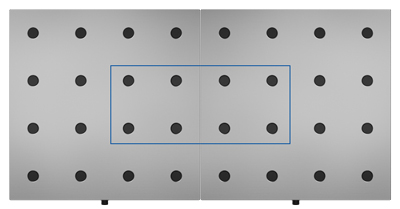
2 Quick•Point® zero-point units This graphic shows an exemplary plate configuration. Other zero-point plate types are also possible.
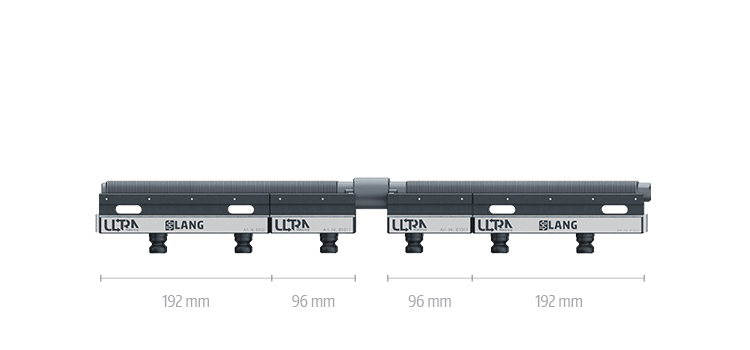
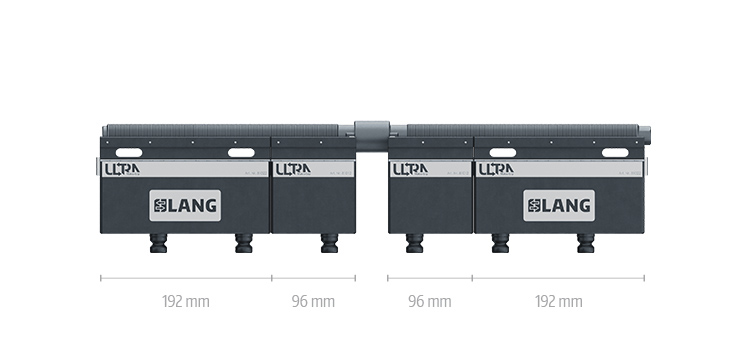

Base Set 610 S
Clamping range up to 610 mm
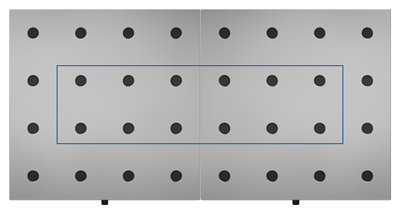
3 Quick•Point® zero-point units This graphic shows an exemplary plate configuration. Other zero-point plate types are also possible.
Base Set 610 M
Clamping range up to 610 mm
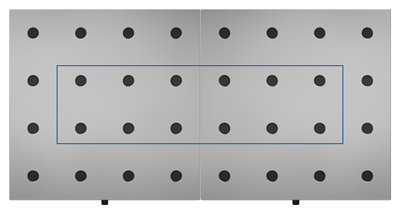
3 Quick•Point® zero-point units This graphic shows an exemplary plate configuration. Other zero-point plate types are also possible.
Base Set 610 L
Clamping range up to 610 mm
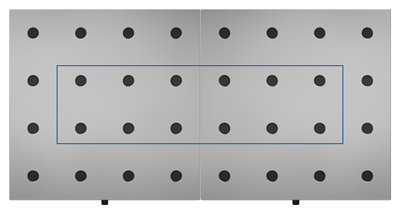
3 Quick•Point® zero-point units This graphic shows an exemplary plate configuration. Other zero-point plate types are also possible.
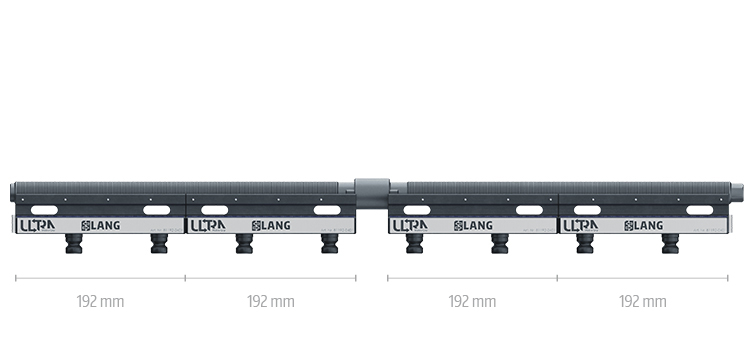
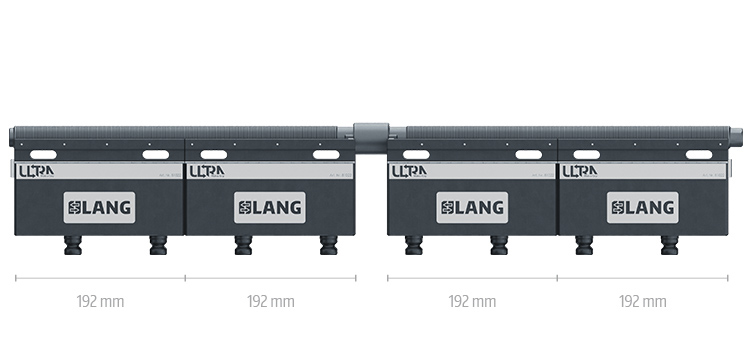
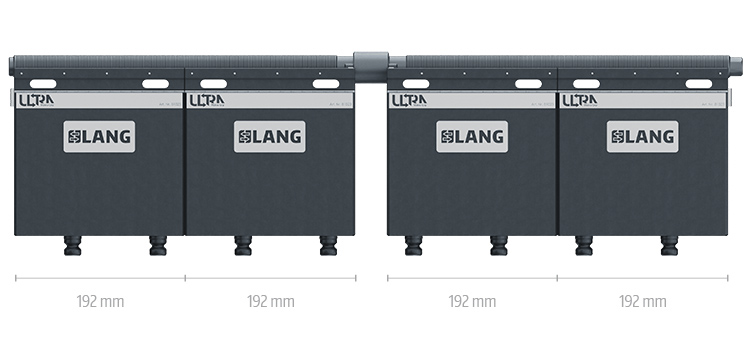
Base Set 810 S
Clamping range up to 810 mm
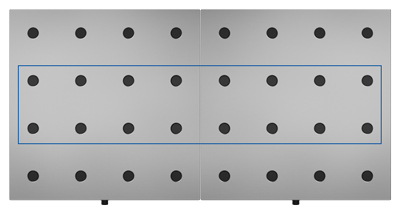
4 Quick•Point® zero-point units This graphic shows an exemplary plate configuration. Other zero-point plate types are also possible.
Base Set 810 M
Clamping range up to 810 mm
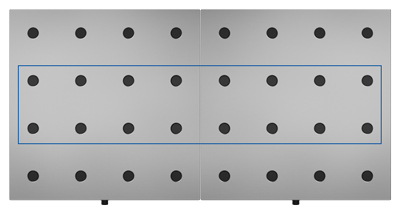
4 Quick•Point® zero-point units This graphic shows an exemplary plate configuration. Other zero-point plate types are also possible.
Base Set 810 L
Clamping range up to 810 mm
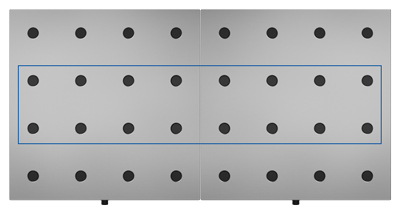
4 Quick•Point® zero-point units This graphic shows an exemplary plate configuration. Other zero-point plate types are also possible.
Base Set includes: Bases with Quick•Point clamping studs, spindle, 2 centering plates, 2 connecting plates (only with Base Sets 610 and 810), Wrenches size 5 and size 19, Quick•Point cover plug remover
Individual components
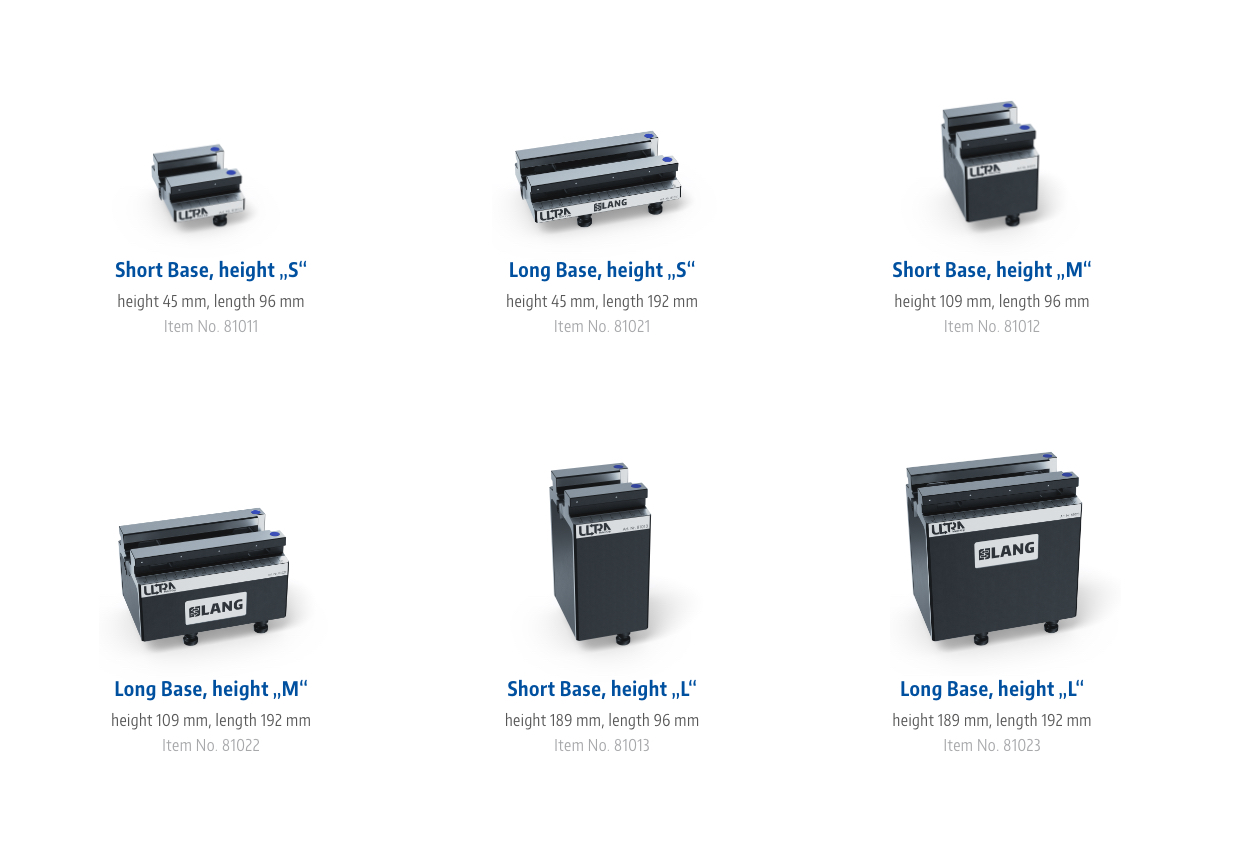
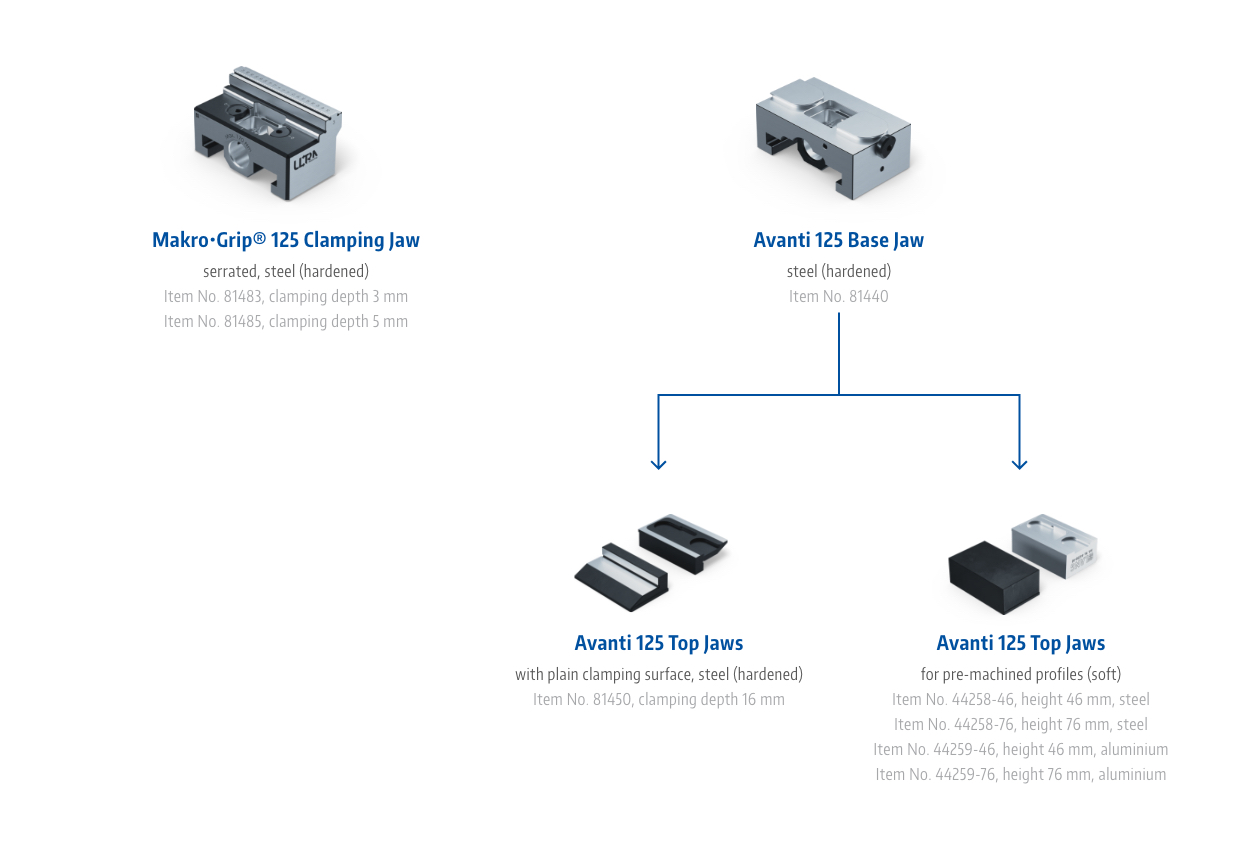
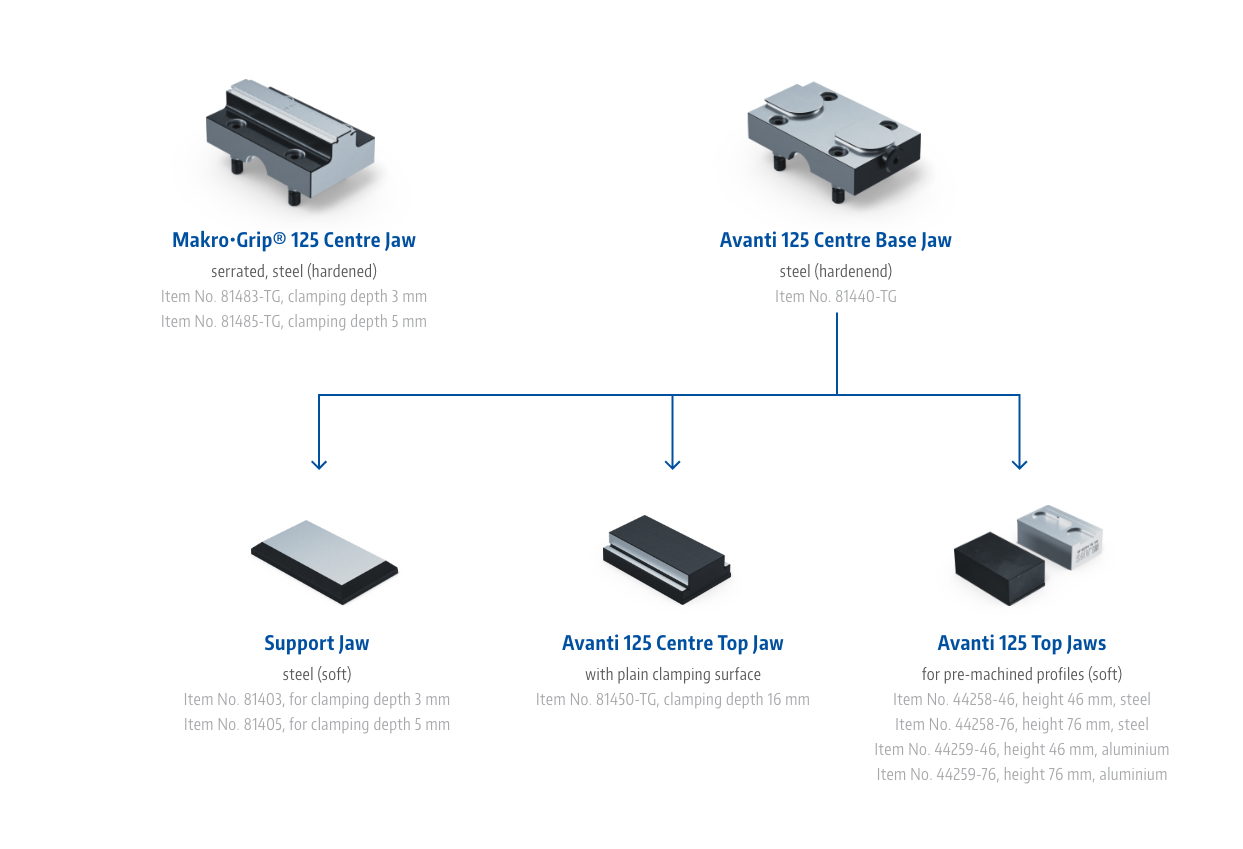
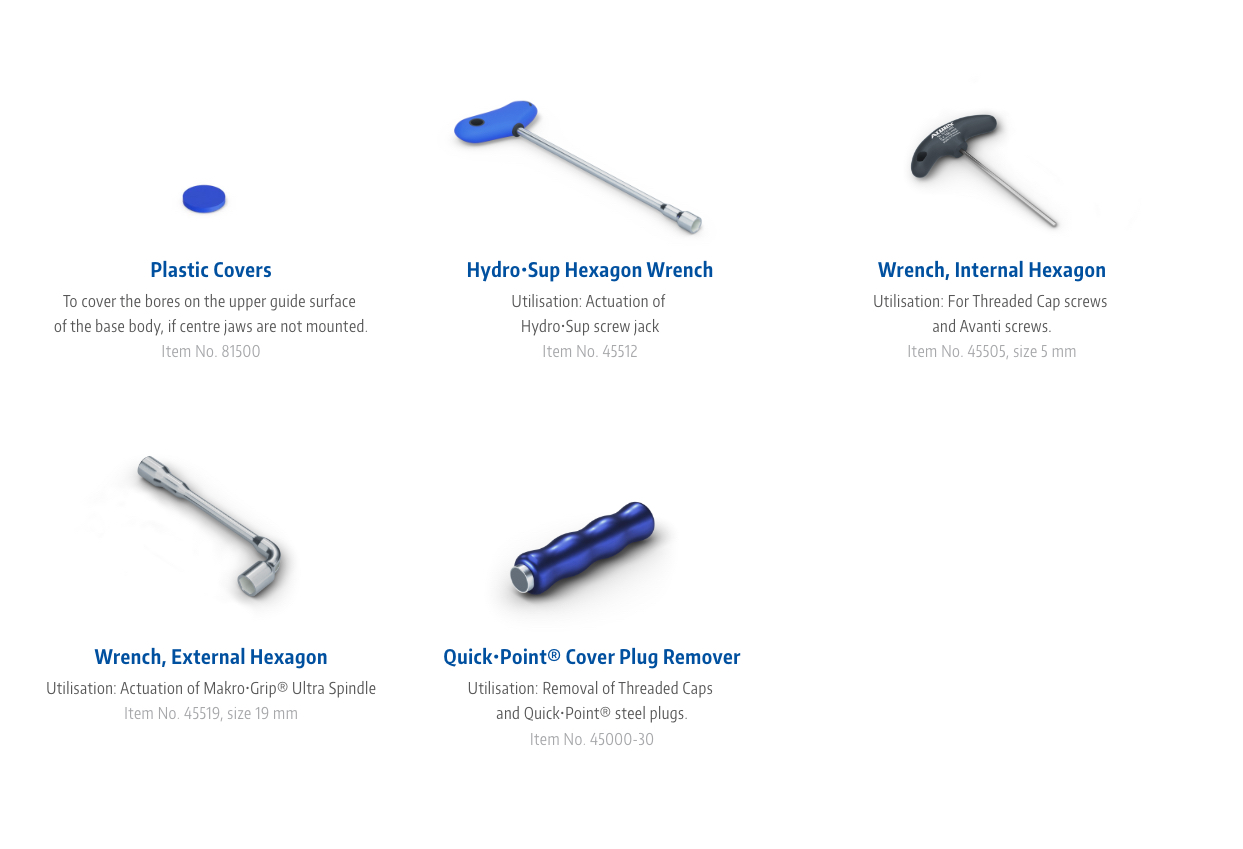
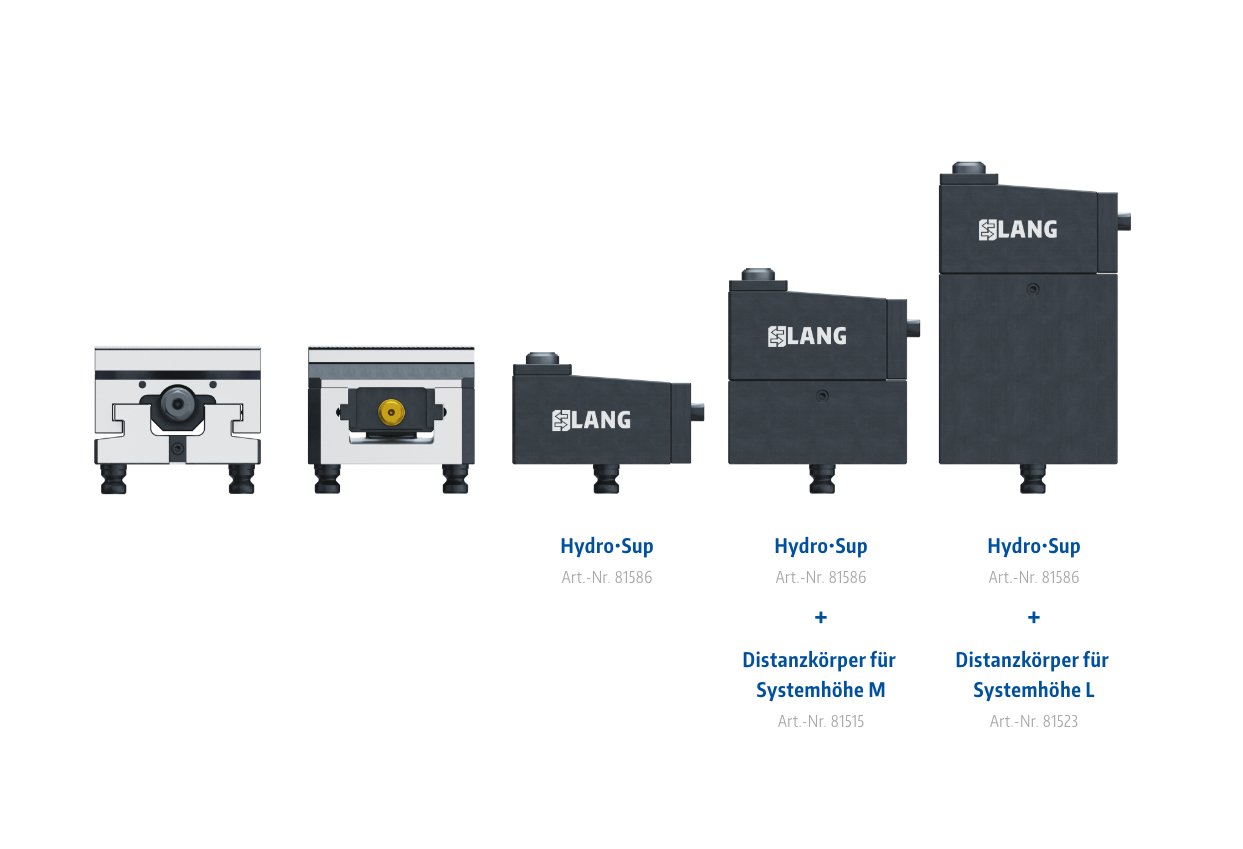
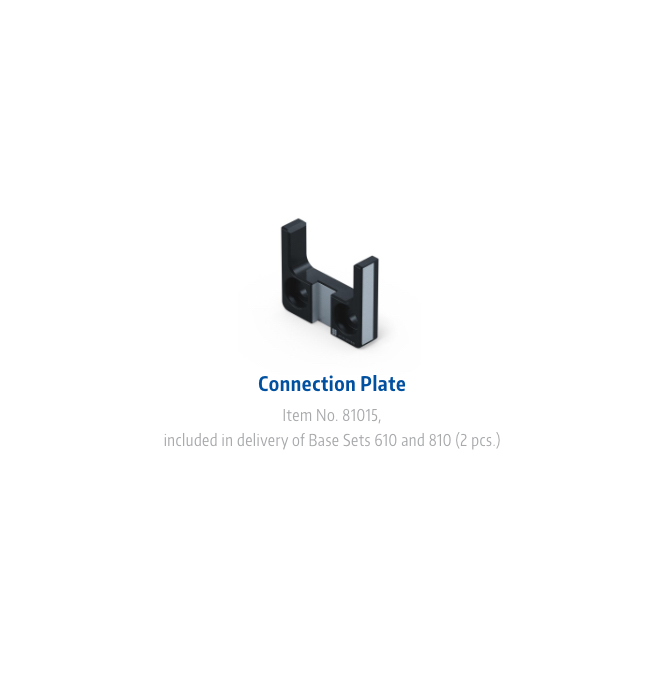
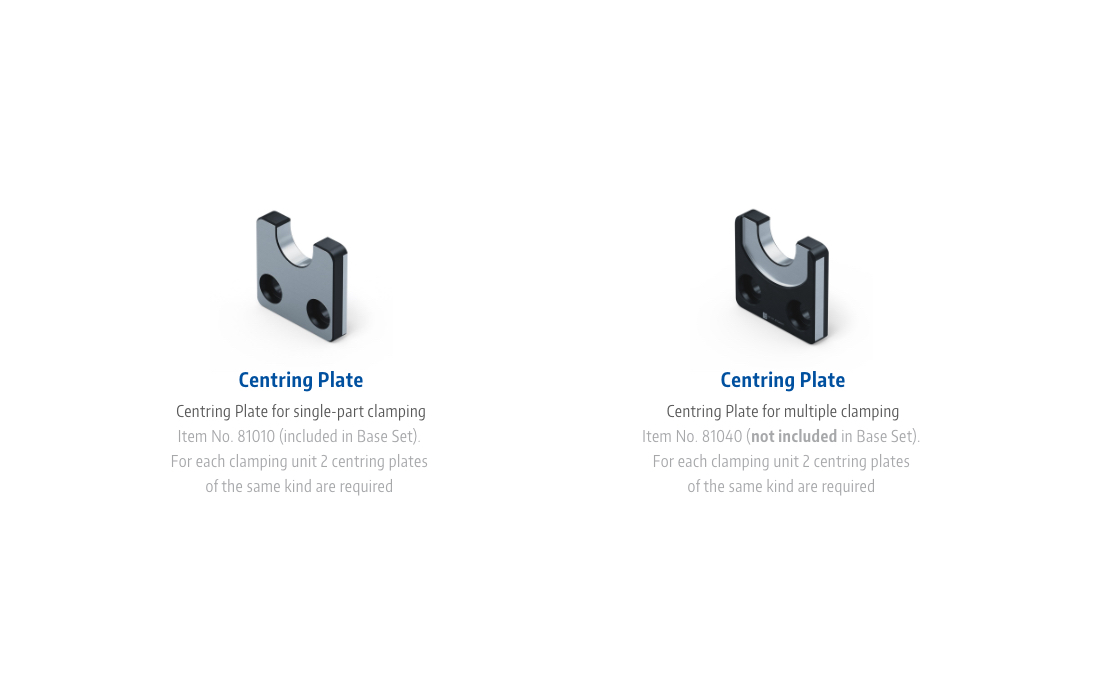
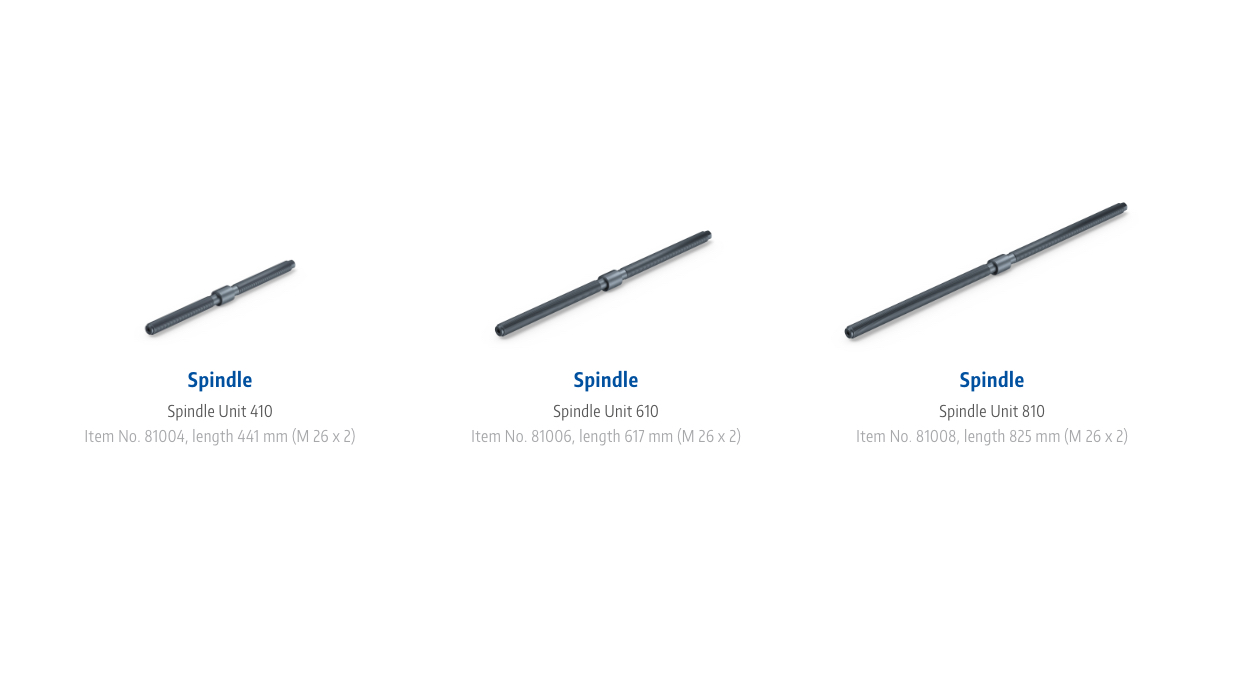
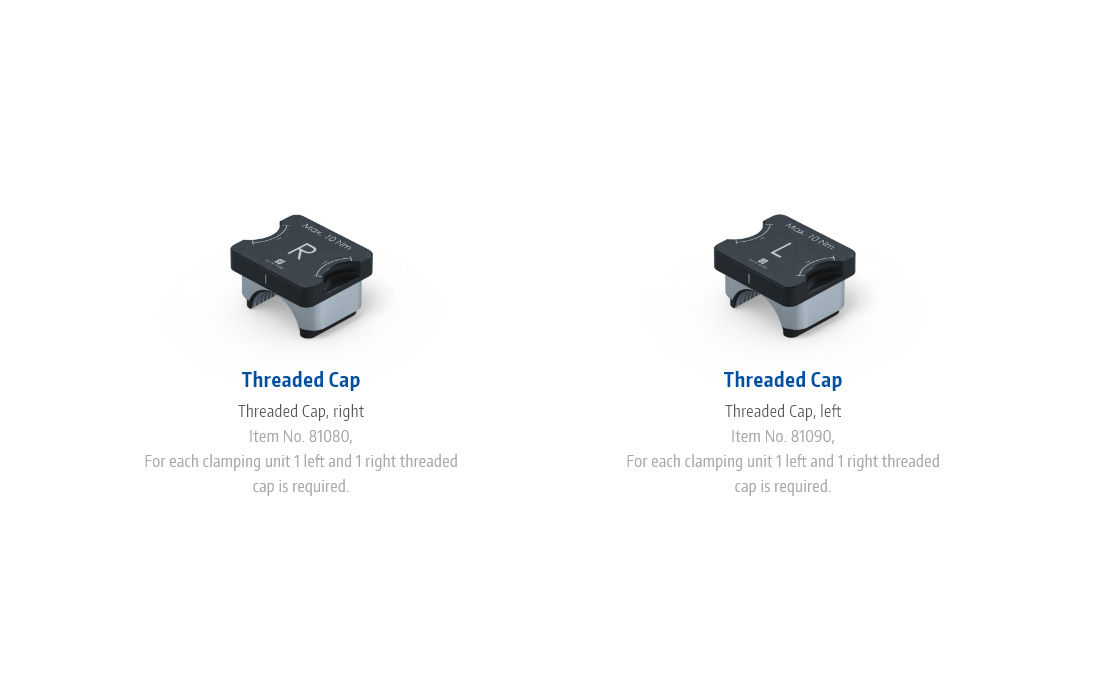
CAD files available to download
Further components of the Base Set
Clamping Jaws
Centre Jaws
Hydro•Sup
Accessories
Makro•Grip® Ultra Stamping Unit
The stamping technology is now available for large parts. The form-closure effect which is made possible by pre-stamping guarantees highest holding forces at low tightening torque. The Makro•Grip® Ultra stamping unit is designed as a dual stamping unit with two stamping vises. These can be flexibly positioned on the grooved plate of the stamping unit in order to precisely reproduce the subsequent clamping situation in the 96 mm grid of the zero point clamping system.
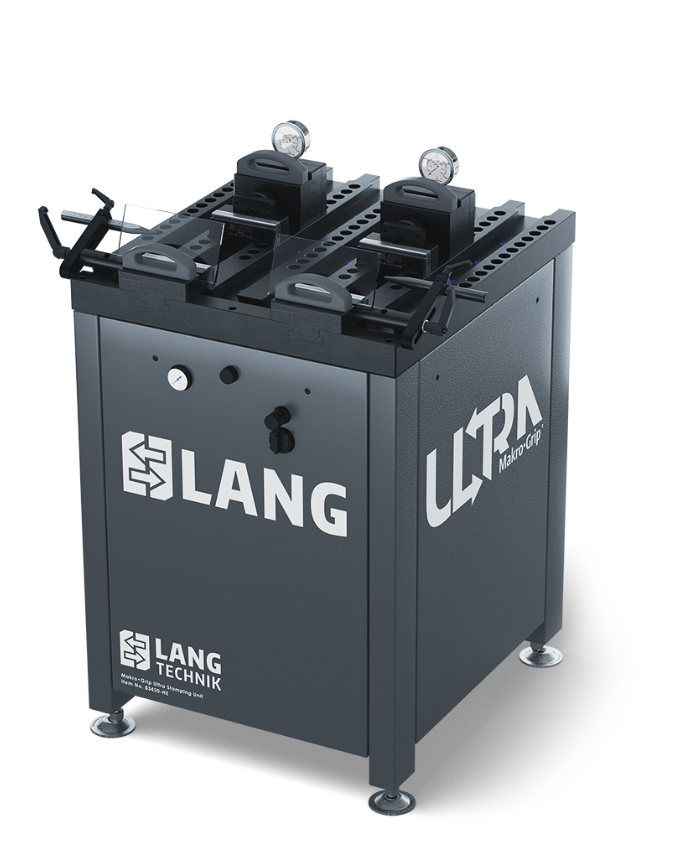
Further information about the Makro•Grip® Ultra stamping unit:
The stamping technology
Form-Closure Technology refers to a technology in which the workpiece to be clamped is “pre-stamped” with a defined contour under high stamping pressure (up to 20 t) outside of the machine tool, before it is clamped in the clamping device. Due to the great amount of advantages for the actual clamping process through “pre-stamping”, the Makro•Grip® technology is considered a benchmark in the 5-sided machining of blanks and absolutely beneficial to automated manufacturing.
More informationWhy pre-stamp a workpiece?
The form-closure effect between the gripping serration of the clamping jaws and stamping indentation guarantees highest holding forces and maximum process reliability at a very low clamping pressure. This practically eliminates any material deformation which is crucial to clamping flat and deformation-sensitive material and a key factor in achieving the desired milling quality. The stamping technology completes the Makro•Grip® Ultra system and raises the quality of plate and large part clamping to a new level.
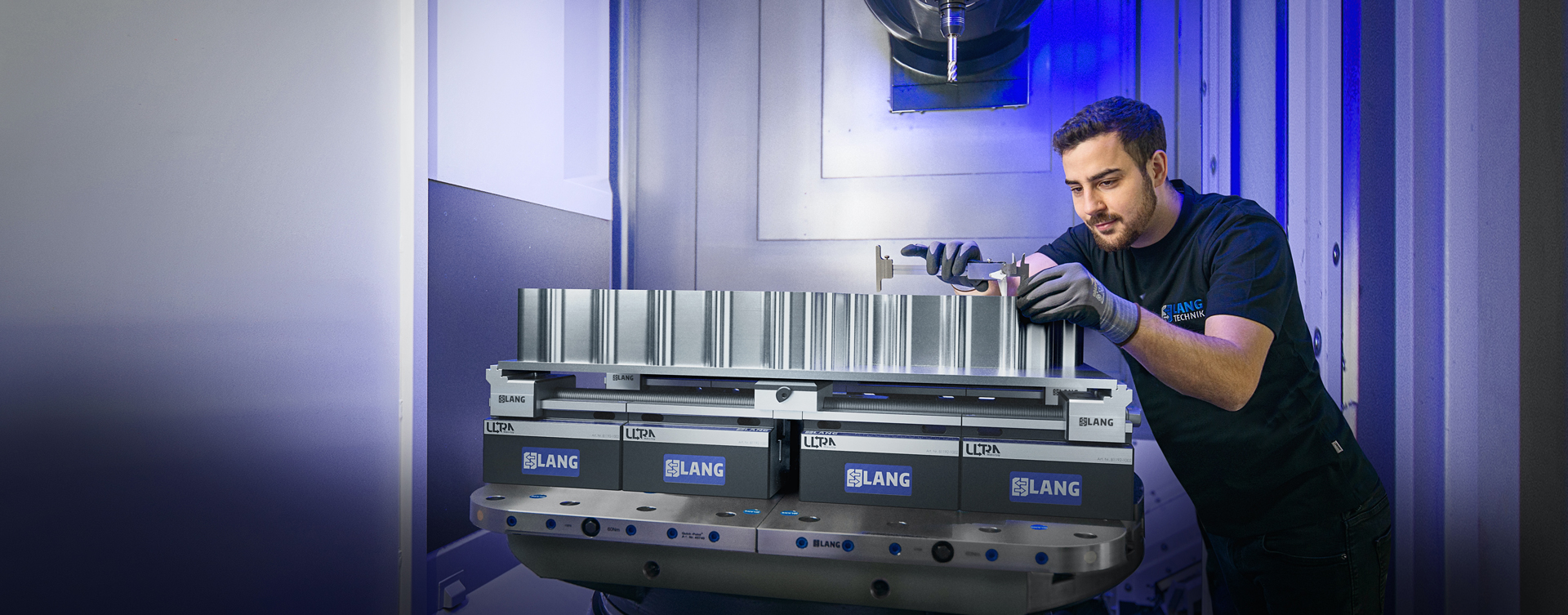
Write your own success story with Makro•Grip® Ultra
Product overviewSuccess Stories
Clamping with Makro•Grip® Ultra pays off according to our customers
Makro•Grip® Ultra offers us the opportunity to clamp components, for which we had no solution so far. I was especially impressed by how fast we were able to solve an existing clamping tasks. From getting to know the system to the first chip in our production it did not even take 3 hours.
Simon Großmann, Großmann Präzisionstechnik, 73235 Weilheim unter Teck, Germany
With the new system by LANG we are now able to clamp large workpieces concentrically. The modularity of Makro•Grip® Ultra combined with the zero-point clamping system made it possible to process various parts in no time. The quick jaw adjustment is designed to be very user-friendly. Also the stamping technology was put to test successfully once again. In this application we clamped a steel block with a height of 350 mm at a clamping depth of only 5 mm. Roughing was done using a high feed milling cutter. With Avanti top jaws the second operation is realized in a few simple steps. In terms of accuracy the LANG system leaves nothing to be desired.
Michael Kupke, MKTec Meisterbetrieb, 86567 Hilgertshausen, Germany
Due to the high level of vertical integration of small batch sizes, set-up times have a significant impact on the economic efficiency in our prototype department. At the same time, the frequent change between different clamping situations demands a lot of flexibility of our workholding. This is exactly where the advantages of the zero-point clamping system and the very modular Makro•Grip® Ultra become apparent for us. Thanks to its modularity, we can always adapt the system exactly to our requirements and cover the majority of parts with basically the same workholding system. We therefore have our setup times under control at all times.
Uwe Herrmann, Bertrandt Technikum GmbH, 71139 Ehningen, Germany
Are you ready to make your production more efficient?
Product overviewLearn more about other solutions by LANG
RoboTrex Automation
RoboTrex covers every need from single part or large-scale production. It is flexible, easy to use and offers best value for money.
More detailsQuick•Point® Zero-Point Clamping System
Flexible, precise and extremely durable – with the modular Quick•Point® system set-up times are reduced to a minimum.
More detailsQuick•Point® Rail quick clamping system
Maximum efficiency with minimum use of resources - the revolutionary quick-clamping system for all machine tables and automation pallets in the CNC milling sector.
More detailsMakro•Grip® Raw Part Clamping and Stamping Technology
Clamping parts by form-closure – For years the Makro•Grip® technology has been the benchmark in the 5-axis machining of raw material.
More detailsHAUBEX Automation System
HAUBEX enables the automatic exchange of the workholding device from the tool magazine with a hood as a carrier system for the vise and workpiece blank.
Learn moreConventional Workholding
Conventional Workholding offers flexible and versatile solutions for clamping round or pre-machined components and contours.
More detailsClean•Tec Chip Fan
The chip fan automatically removes chips and coolant from machine tables, fixtures and workpieces after the machining process.
More details